The tubing size, specifically the inner diameter (ID), significantly influences the flow rate and dosing accuracy in peristaltic pump systems.
Here’s how tubing size affects these factors:
- Flow Rate:
- Larger ID Tubing: Using tubing with a larger inner diameter allows for a higher flow rate. This is because there is more space for the fluid to pass through. If a higher flow rate is required for a particular application, larger ID tubing should be used.
- Smaller ID Tubing: Smaller ID tubing restricts the flow path, resulting in a lower flow rate. It is suitable for applications where a slower flow rate is needed to avoid splashing, shearing, or over-dispensing.
- Dosing Accuracy:
- Larger ID Tubing: While larger ID tubing allows for higher flow rates, it can be less precise when it comes to dosing accuracy. The flow may be less predictable, making it more challenging to achieve precise dosing.
- Smaller ID Tubing: Smaller ID tubing provides finer control over the flow rate, leading to improved dosing accuracy. This is important for applications that require precise measurements and where even small variations in flow rate can impact the outcome.
- Viscous Fluids:
- Viscous fluids, such as thick liquids or slurries, can be challenging to pump. Larger ID tubing is often chosen for such fluids to reduce resistance and facilitate flow. However, it’s essential to strike a balance between flow rate and dosing accuracy.
- Compatibility with Pump System:
- The choice of tubing size should also consider the compatibility with the pump system’s design. Some peristaltic pumps may be optimized for specific tubing sizes. Using the recommended tubing size ensures optimal performance.
- Application Requirements:
- The specific requirements of the application should guide the selection of tubing size. Consider factors such as the desired flow rate, dosing accuracy, fluid properties, and any safety or contamination concerns when choosing the appropriate tubing size.
In summary, tubing size, particularly the inner diameter, is a critical parameter in peristaltic pump systems. It directly affects the flow rate and dosing accuracy. The choice of tubing size should be made with a clear understanding of the application’s needs and the trade-offs between flow rate and dosing precision. It’s also important to consider the characteristics of the fluid being pumped, as well as any specific pump system requirements.
What factors influence the service life and durability of peristaltic pump tubing, and what maintenance practices can extend the tubing’s longevity?
The service life and durability of peristaltic pump tubing are influenced by several factors, and there are maintenance practices that can extend the tubing’s longevity.
Here are key factors and maintenance practices to consider:
Factors Influencing Tubing Life:
- Tubing Material: The choice of tubing material is a critical factor. Different materials have varying resistance to wear, chemical compatibility, and temperature tolerance. Select a tubing material that matches the demands of the application.
- Fluid Properties: The properties of the fluid being pumped, such as its viscosity, abrasiveness, and chemical composition, can affect tubing wear. Highly abrasive or corrosive fluids may lead to faster tubing degradation.
- Pump Speed: The pump speed can influence tubing life. Excessive speed may lead to quicker wear and reduced tubing life. Adjust the pump speed to balance flow rate with tubing longevity.
- Tubing Flexibility: Tubing flexibility impacts its resilience. More flexible tubing materials can withstand the repeated compression and decompression of peristaltic action without as much wear and fatigue.
- Tubing Size: Smaller tubing sizes may wear out faster than larger sizes due to the increased stress China Peristaltic Pump Tubing manufacturers on the tubing material. Select the appropriate tubing size for the application’s flow rate requirements.
- Environmental Conditions: Temperature, humidity, and exposure to UV radiation can impact tubing life. Ensure that the tubing material is suitable for the application’s environmental conditions.
- Maintenance Practices: Regular maintenance and proper care can significantly extend tubing life. Proper maintenance practices include:
Maintenance Practices to Extend Tubing Life:
- Inspect Tubing: Regularly inspect the tubing for signs of wear, cracks, or abrasions. Replace tubing at the first signs of damage to prevent leaks or contamination.
- Lubrication: Some peristaltic pumps benefit from lubricating the tubing with a suitable lubricant. Check the manufacturer’s recommendations for lubrication practices.
- Proper Storage: Store tubing in a clean, dry, and dark environment to protect it from environmental factors and UV radiation. Avoid kinking or crimping the tubing during storage.
- Tubing Replacement: Follow a schedule for tubing replacement based on the manufacturer’s recommendations or the tubing’s wear and tear. This helps prevent unexpected tubing failures.
- Tubing Flushing: Regularly flush the tubing with a compatible cleaning solution to remove any residue or buildup that can accelerate wear.
- Pump Calibration: Calibrate the pump to ensure accurate dosing, reducing the need for excessive tubing wear due to repeated adjustments.
- Pump Speed Adjustment: Optimize the pump speed to balance flow rate with tubing life. Avoid excessive speeds that may lead to tubing fatigue.
- Use Tubing Retainers: Some applications benefit from the use of tubing retainers or guides that reduce stress on the tubing during the peristaltic action.
- Proper Tubing Installation: Follow the manufacturer’s guidelines for tubing installation to ensure it’s properly seated and free from kinks or twists.
- Safety Measures: Implement safety measures to prevent overpressurization, splashing, or other conditions that may lead to tubing wear or rupture.
By considering these factors and implementing appropriate maintenance practices, you can extend the service life and durability of peristaltic pump tubing, ensuring reliable and cost-effective fluid handling in your applications.
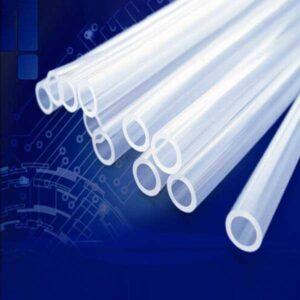