To determine the optimal tubing size for a peristaltic pump to achieve the desired flow rate while maintaining dosing accuracy, users should consider several factors and perform the following steps:
- Understand Your Application Requirements:
- Start by understanding the specific needs of your application, including the required flow rate, dosing accuracy, and the properties of the fluid being pumped.
- Consult the Pump Manufacturer:
- Reach out to the manufacturer of your peristaltic pump for guidance. They can provide recommendations and guidelines for selecting the most appropriate tubing size for your specific pump model.
- Consider Fluid Properties:
- Take into account the viscosity, chemical compatibility, and other properties of the fluid. High-viscosity fluids may require larger tubing sizes to accommodate the flow, while low-viscosity fluids can work with smaller tubing.
- Evaluate Tubing Materials:
- Choose a tubing material that is compatible with the fluid being pumped. Different materials have varying properties, including resistance to wear, chemical compatibility, and temperature tolerance.
- Calculate Flow Rate Requirements:
- Calculate the desired flow rate for your application. You can use flow rate equations or consult relevant technical references. The flow rate may be specified in mL/min, L/hr, or other appropriate units.
- Review Tubing Size Options:
- The manufacturer or supplier of peristaltic pump tubing typically provides a range of tubing sizes with different inner diameters (ID). Review the available tubing sizes to find the options that match your desired flow rate.
- Perform Flow Rate Testing:
- Conduct flow rate testing with different tubing sizes to determine which size meets your flow rate requirements. This can involve setting up the pump with each tubing size and measuring the actual flow rate.
- Assess Dosing Accuracy:
- Evaluate the dosing accuracy achieved with each tubing size during testing. Ensure that the selected tubing size provides the required level of dosing precision for your application.
- Consider Safety and Contamination Risks:
- Take into account any safety or contamination risks associated with the flow rate and tubing size. For example, higher flow rates might increase the risk of splashing or aerosol formation, which can be a safety concern.
- Balance Flow Rate and Dosing Accuracy:
- Find the tubing size that strikes the right balance between flow rate and dosing accuracy. Smaller tubing sizes provide better dosing accuracy but may limit the flow rate, while larger tubing sizes can achieve higher flow rates but may sacrifice some dosing precision.
- Perform Long-Term Testing:
- Conduct long-term testing with the selected tubing size to ensure it maintains its performance and dosing accuracy over an extended period. This helps confirm the suitability of the chosen size for your application.
- Document and Monitor:
- Keep records of your tubing size selection and the results of flow rate and dosing accuracy testing. Monitor the tubing’s condition and performance over time to ensure it continues to meet your application requirements.
By following these steps and carefully considering all relevant factors, users can select the optimal tubing size for their peristaltic pump, achieving the desired flow rate while maintaining dosing accuracy and ensuring the success of their specific application.
What is peristaltic pump tubing, and how does it play a critical role in the operation of peristaltic pumps?
Peristaltic pump tubing is an essential component in the operation of peristaltic pumps. It plays a critical role in facilitating the movement of fluids within the pump system. Peristaltic pumps, often referred to as tubing pumps or hose pumps, work based on the peristaltic principle, which involves the compression and relaxation of a flexible tube or hose.
Here’s an overview of peristaltic pump tubing and its role:
Peristaltic Pump Tubing:
- Peristaltic pump tubing is typically made of flexible and resilient materials, such as various types of elastomers or thermoplastics. The tubing is designed to be highly resistant to wear, chemicals, and temperature extremes, making it suitable for a wide range of applications.
Role in the Operation of Peristaltic Pumps:
Peristaltic pump tubing plays a critical role in the operation of peristaltic pumps through the following key functions:
- Peristaltic Action: Peristaltic pumps rely on the peristaltic action to move fluids. This action involves the sequential compression and relaxation of the tubing along its length. As the pump’s rotor or rollers press against the tubing, they create a series of occlusions (squeezing) and relaxations (releasing) that push the fluid along the tubing.
- Positive Displacement: Peristaltic pumps are positive displacement pumps, meaning they deliver a precise and consistent volume of fluid with each compression cycle. The tubing serves as the positive displacement element by capturing and transporting the fluid without any direct contact between the fluid and the pump’s components. This feature makes peristaltic pumps highly accurate for dosing and metering applications.
- Isolation and Contamination Prevention: The tubing isolates the fluid from the pump’s internal components, eliminating the risk of contamination or interaction China Peristaltic Pump Tubing suppliers between the fluid and the pump’s materials. This is particularly valuable when handling sensitive or aggressive fluids.
- Compatibility: The choice of tubing material is essential for compatibility with the fluid being pumped. Peristaltic pump tubing is available in a wide range of materials, including silicone, PVC, Viton, and others, to accommodate various fluid properties and applications.
- Ease of Maintenance: Peristaltic pump tubing is a replaceable component, making maintenance straightforward. When the tubing becomes worn or damaged, it can be easily replaced without requiring extensive maintenance or downtime for the entire pump system.
- Reduced Contamination Risk: Because there is no backflow or contact between the fluid and the pump’s internal components, the risk of contamination or cross-contamination is minimized. This is crucial in applications where maintaining the purity and integrity of the fluid is paramount.
In summary, peristaltic pump tubing is the workhorse of the peristaltic pump system, responsible for displacing and transporting fluids accurately, reliably, and safely. Its flexibility, compatibility with various materials, and ease of replacement make it a critical element in the functioning of peristaltic pumps across a wide range of industries and applications, including pharmaceuticals, biotechnology, water treatment, and chemical processing.
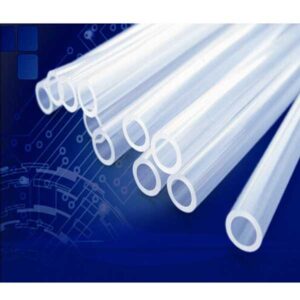